Universal Joint Vs Drive Shaft Coupler – Which is Right for You?
When it comes to mechanical systems, selecting the right power transmission component can make all the difference in performance and longevity. Two commonly encountered solutions are universal joints and drive shaft couplers, yet many professionals and hobbyists struggle to determine which is best suited for their application. Both serve to connect rotating shafts, but their designs, capabilities, and use cases vary significantly. This article delves into the distinctions between universal joints and drive shaft couplers, guiding you through their functions, advantages, and ideal applications to help you make an informed decision.
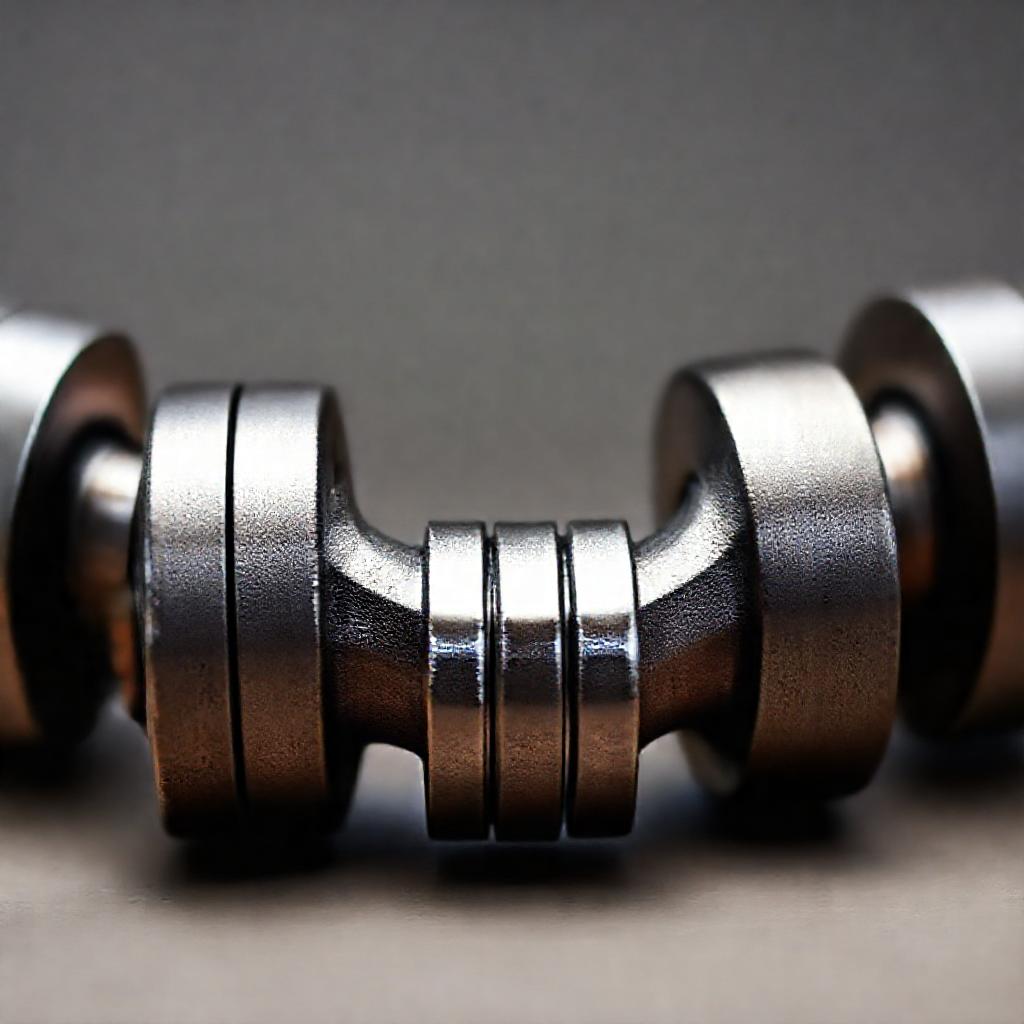
Understanding Universal Joints
What Is a Universal Joint?
Universal joints, often referred to as U-joints, are mechanical couplings designed to transmit rotational motion between two shafts that are not in a straight line. They are particularly useful when there is angular misalignment, allowing rotational movement even when the shafts are at an angle. The term “universal” comes from their ability to work in various orientations, a feature that has made them indispensable since their inception in the early 20th century.
Structure and How It Works
A universal joint consists of a cross-shaped yoke, bearings, and grease fittings. This design enables it to compensate for angular misalignment in non-parallel shafts by allowing rotational flexibility at each end. The joint operates by transferring torque through its cross and bearings, making it ideal for systems that require motion in multiple planes.
Common Applications
Universal joints are widely used in automotive drive shafts, industrial machinery, and aerospace systems. They are especially valued in vehicles for connecting the transmission to the rear axle, where angular movement is inevitable. Their high torque capacity makes them suitable for heavy-duty applications like construction equipment and agricultural machinery.
Pros and Cons of Universal Joints
- Pros: High torque capacity, compact design, accommodates angular misalignment.
Drive Shaft Couplers Explained
What Is a Drive Shaft Coupler?
A drive shaft coupler is a mechanical device that connects two shafts to transmit rotational power while compensating for misalignment. Unlike universal joints, couplers focus on maintaining alignment and minimizing vibration, ensuring smoother operation in systems where precision is critical.
Types of Drive Shaft Couplers
Drive shaft couplers come in flexible and rigid variants. Flexible types, such as jaw, beam, and gear couplers, handle axial, radial, and angular misalignment by using elastic elements or adjustable designs. Rigid couplers, on the other hand, are best for systems where shafts are already aligned and require no compensation.
Key Metrics
Performance metrics for Universal Joint Vs Drive Shaft Coupler – Which is Right for You?
Common Applications
Drive shaft couplers are commonly found in pumps, compressors, generators, and conveyors. They are preferred in industrial settings where maintaining alignment and reducing mechanical stress is essential, such as in HVAC systems and marine propulsion units.
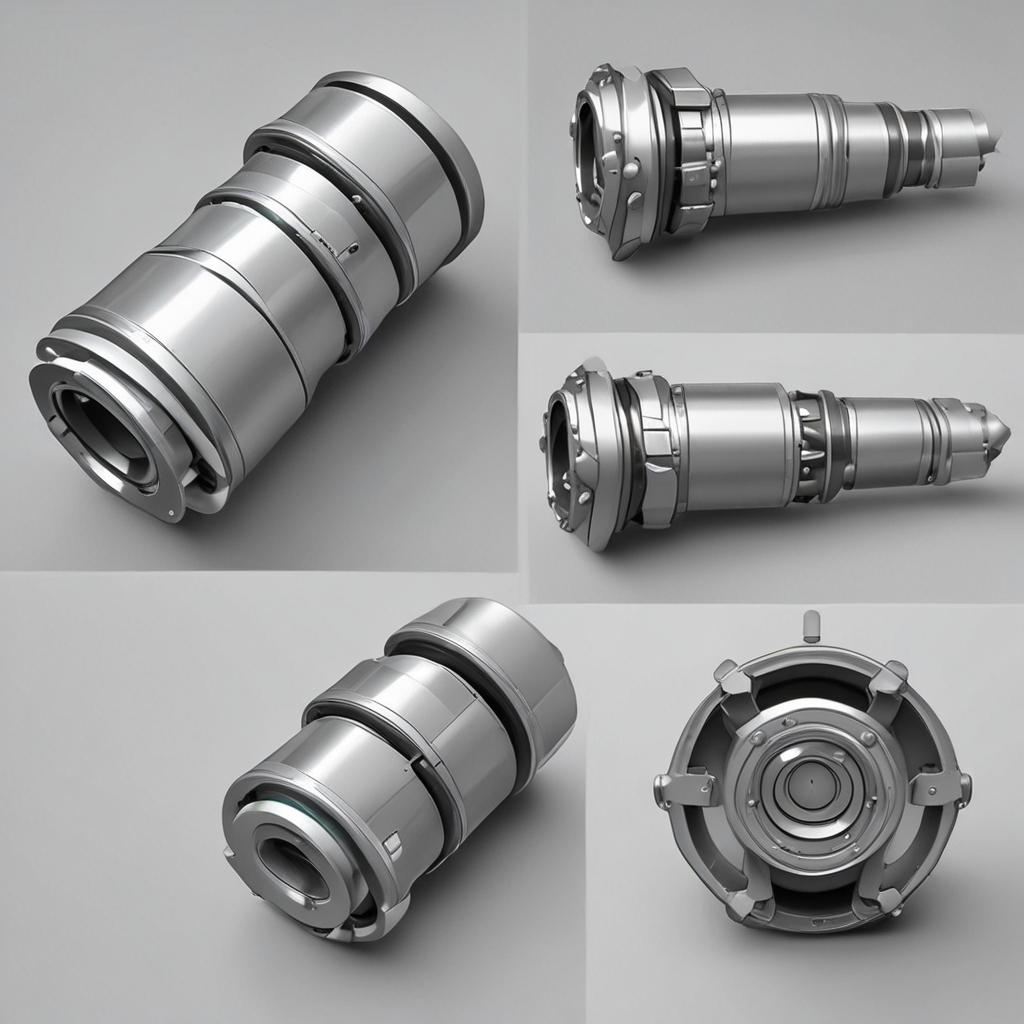
Pros and Cons of Drive Shaft Couplers
- Pros: Low maintenance, reduces vibration, versatile for various misalignment types.
Key Differences Between Universal Joints and Drive Shaft Couplers
Function and Design Variations
The primary difference lies in how each component handles misalignment. Universal joints excel in angular misalignment but are limited in flexibility, while drive shaft couplers, especially flexible ones, address axial, radial, and angular misalignment. Structurally, U-joints use a cross-shaped yoke and bearings, whereas couplers often feature single-piece or split designs with elastic or metallic components.
Performance in Dynamic vs. Static Systems
Universal joints are ideal for dynamic systems like automotive drive shafts that experience constant motion and high torque. Drive shaft couplers perform better in static or semi-static systems, such as industrial pumps, where maintaining precise alignment and reducing vibration are more critical than extreme angular flexibility.
Cost and Maintenance Considerations
Universal joints generally have a higher upfront cost but require frequent lubrication and inspections, increasing long-term expenses. Drive shaft couplers often prove more cost-effective over time due to their low-maintenance nature, though specialized models can be expensive initially. Both may involve downtime for repairs, but U-joints typically demand more hands-on care.
Industry-Specific Use Cases
Automotive and heavy machinery industries rely on universal joints for their ability to handle angular shifts and high torque. Drive shaft couplers are preferred in HVAC, marine, and precision manufacturing equipment where smooth power transfer and alignment stability are prioritized. Environmental factors like extreme temperatures or heavy loads also tilt the choice toward one component over the other.
How to Decide: Universal Joint vs Drive Shaft Coupler
Assessing Your System’s Requirements
Begin by evaluating torque requirements, speed, and the type of misalignment your system experiences. For angular misalignment in high-torque environments, a universal joint is likely the right choice. If your application involves multidirectional misalignment or precision alignment, a drive shaft coupler will perform better. Consulting manufacturer specifications can clarify these needs further.
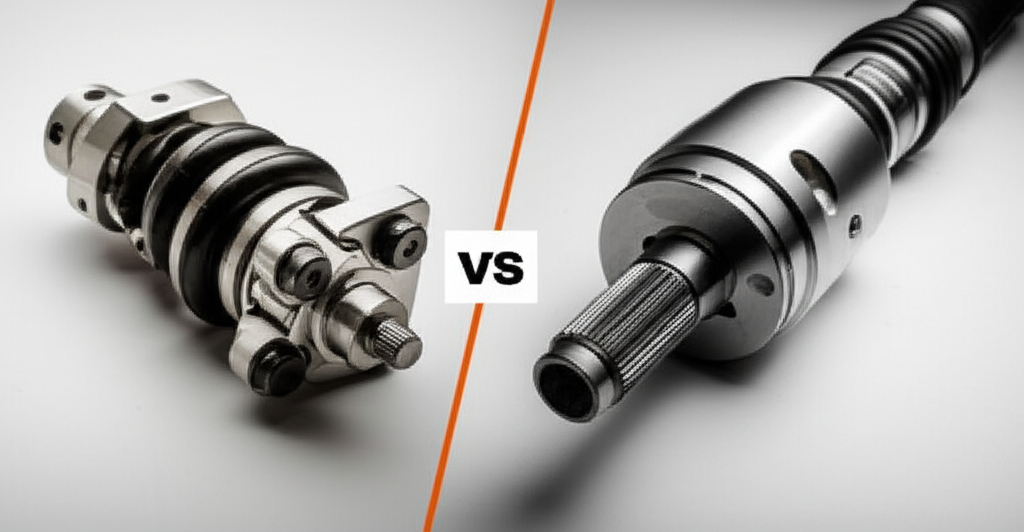
Budget and Cost Efficiency
Drive shaft couplers may offer long-term savings due to minimal maintenance, while universal joints can incur higher costs from regular servicing and potential early replacements. However, the initial investment in high-quality couplers should not be overlooked, especially in critical systems where failure is costly.
Maintenance and Operational Longevity
Universal joints need periodic lubrication and inspections to prevent bearing wear, whereas drive shaft couplers require less frequent attention but may degrade from material fatigue in high-vibration settings. Opt for durable materials and designs that align with your system’s operational demands to maximize lifespan and reduce downtime.
Frequently Asked Questions (FAQ)
What’s the main difference between a universal joint and a drive shaft coupler?
The primary distinction is their ability to handle misalignment. Universal joints accommodate angular misalignment between non-parallel shafts, while drive shaft couplers, particularly flexible types, manage axial, radial, and angular misalignment through adaptable designs.
Can I use a universal joint and a drive shaft coupler interchangeably?
No, they are not interchangeable. Universal joints are unsuitable for multidirectional misalignment beyond their design limits, and couplers lack the torque capacity for applications requiring high rotational force. Using the wrong component can lead to mechanical failure or reduced efficiency.
Which component is more durable in high-vibration environments?
Drive shaft couplers are generally more durable in high-vibration settings because they are engineered to absorb shocks and reduce stress. Universal joints, however, are prone to bearing wear in such conditions, requiring more frequent maintenance to avoid breakdowns.
In which industries are drive shaft couplers preferred over universal joints?
Drive shaft couplers are favored in HVAC systems, marine applications, and precision manufacturing due to their vibration-dampening properties and alignment stability. They are also common in pumps and generators where smooth operation is key.
How much does it replace a universal joint or drive shaft coupler?
Replacement costs vary widely. Universal joints typically range from $50 to $300 depending on size and material, while drive shaft couplers can cost between $100 and $500 for industrial-grade models. Brand reputation and customization needs further influence pricing.
Conclusion: Making the Right Choice for Your Mechanical System
Selecting between a universal joint and a drive shaft coupler hinges on understanding your system’s unique demands. For dynamic setups that require high torque and angular flexibility, universal joints remain the gold standard. In contrast, drive shaft couplers are better suited for static applications where vibration reduction and precise alignment are critical. Always consider factors like maintenance frequency, environmental conditions, and budget when choosing. For complex systems, collaborating with an engineer or supplier can provide tailored insights to ensure optimal performance and longevity.