Grease Fittings
Grease fittings are small but vital components in the world of machinery and vehicles, acting as the gateway for lubrication to critical moving parts. Often overlooked, these fittings ensure that bearings, joints, and other mechanical elements stay well-lubricated, reducing friction, heat, and wear. Proper use and maintenance of grease fittings can significantly extend the life of expensive equipment, prevent costly breakdowns, and maintain operational efficiency. Whether in automotive, manufacturing, or construction settings, selecting and caring for these fittings is essential for smooth and reliable performance.
What Are Grease Fittings?
Grease fittings, also known as grease nipples or zerks, are threaded valves designed to deliver lubricant to machinery components. They allow controlled application of grease via a grease gun, ensuring that moving parts remain properly coated and protected from debris. By channeling lubricant precisely to bearings, pivots, and joints, grease fittings play a key role in minimizing mechanical stress and breakdowns.
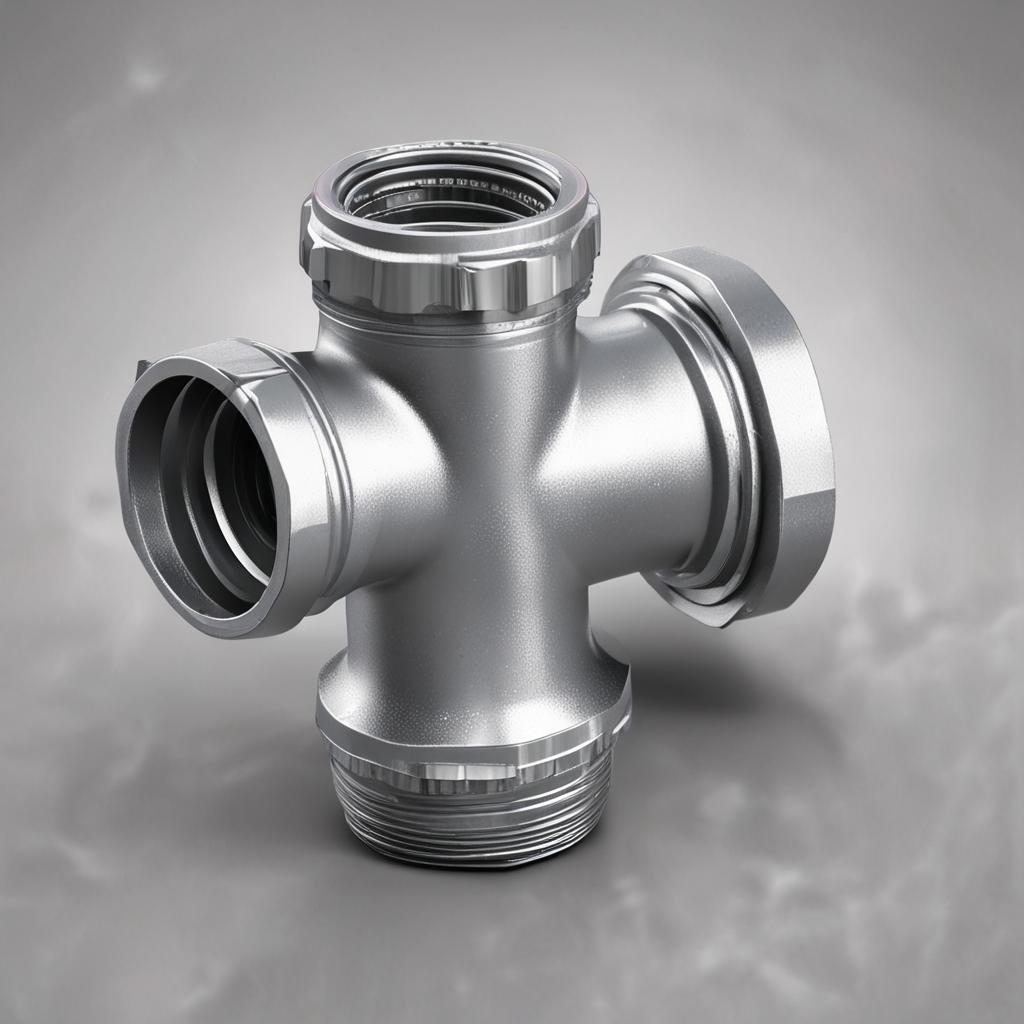
These fittings are ubiquitous across industries. In automotive settings, they lubricate wheel hubs and suspension parts. Manufacturing plants rely on them for conveyor systems and assembly line machinery. Construction equipment, such as excavators and cranes, also depends on grease fittings to keep joints functioning smoothly under heavy loads.
Types of Grease Fittings
Standard Grease Fittings (Zerks)
Standard grease fittings are the most common type, typically made of steel, brass, or stainless steel. They feature a 45-degree angle and a 1/8″ NPT thread size, suitable for light to moderate lubrication needs. These fittings are ideal for everyday use in vehicles and machinery with lower pressure requirements.
Applications include automotive ball joints, bicycle hubs, and small industrial equipment. Their widespread use is due to their affordability and ease of access, though they may not withstand extreme conditions without regular maintenance.
High-Pressure Grease Fittings
Engineered for heavy-duty tasks, high-pressure grease fittings are built to handle pressures up to 3,000 psi or more. They often use reinforced materials like brass or stainless steel and have thicker walls to prevent leakage or failure under stress. These fittings are designed for machinery that demands consistent, powerful lubrication.
Common in mining, construction, and large-scale industrial equipment, they are essential for components like track rollers, hydraulic motors, and high-load bearings. Their durability makes them a top choice for environments where equipment operates continuously and under intense pressure.
Hydraulic Grease Fittings
Hydraulic grease fittings are specialized for use in hydraulic systems. They feature threaded designs that prevent contamination from dust and moisture, ensuring the integrity of hydraulic grease. These fittings are typically compatible with thick, high-viscosity greases used in hydraulic components.
Used in hydraulic cylinders, pumps, and valves, they help maintain system efficiency by keeping lubricants clean and static parts sealed. Their construction often includes a non-return valve to prevent backflow and leakage when the system is inactive.
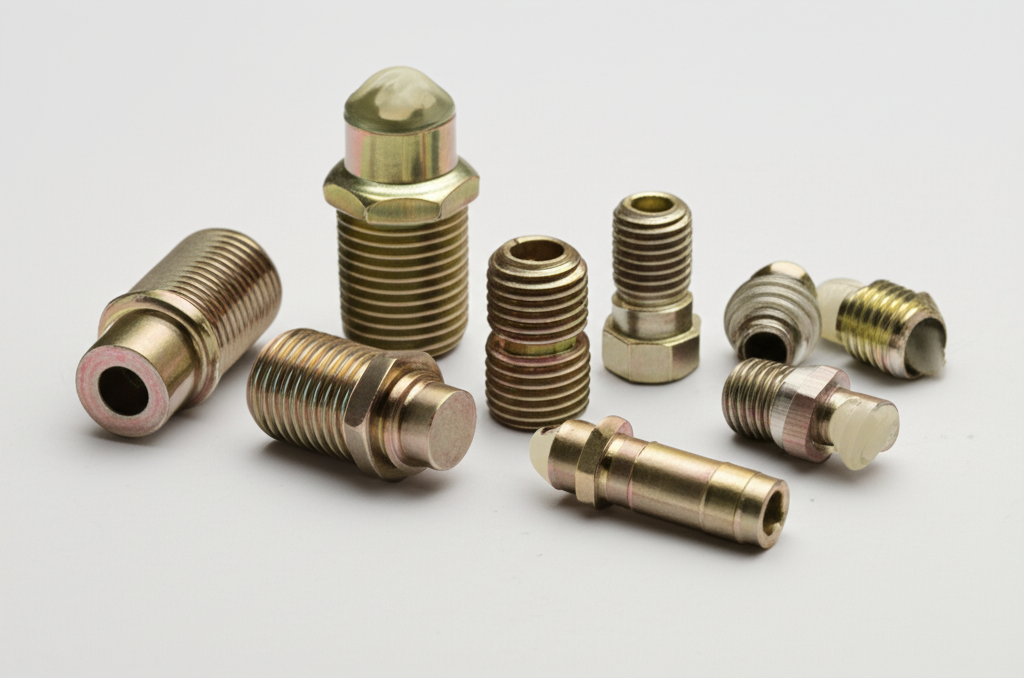
Push-to-Connect Grease Fittings
Push-to-connect fittings simplify installation by eliminating the need for threading. Users simply press the fitting onto the lubrication port, making them ideal for quick maintenance tasks. They are popular in automotive and light machinery applications for their convenience.
Pros include faster installation and reduced risk of cross-threading. However, they may not suit high-pressure systems and can be prone to accidental disconnection. These fittings are best for low-stress components like door hinges or small equipment joints.
Heavy-Duty Industrial Grease Fittings
Heavy-duty fittings are built for harsh environments, featuring robust materials such as stainless steel or nickel-plated brass. They resist corrosion, extreme temperatures, and physical damage, making them suitable for demanding industrial settings. These fittings are often used in chemical plants, steel mills, and other high-stress manufacturing environments.
Applications include gearboxes, rotating shafts, and equipment exposed to moisture or chemicals. Their design ensures long-term reliability even in conditions where standard fittings would fail prematurely.
How to Choose the Right Grease Fitting
Selecting the correct grease fitting involves evaluating several factors. Size is critical—1/8″ NPT is standard, but larger sizes may be needed for heavy-duty applications. Material choice depends on the environment: stainless steel for corrosion resistance, brass for cost-effectiveness, and steel for structural strength. Pressure requirements and compatibility with specific grease types are also key considerations.
For example, lithium-based greases work well with standard fittings, while synthetic or high-viscosity greases may require hydraulic or high-pressure options. Always consult machinery specifications to ensure alignment with the correct fitting type and lubricant.
Installation and Maintenance of Grease Fittings
Proper Installation Techniques
Installing grease fittings requires a grease gun and a fitting wrench. Begin by cleaning the installation port to remove dirt or old grease. Align the threads carefully to avoid cross-threading, then tighten the fitting securely without over-torquing. Always verify compatibility with the lubrication system before installation.
Common mistakes include using undersized fittings or neglecting to check for damaged threads. A poorly installed fitting can lead to leaks or inadequate lubrication, potentially causing equipment failure. Take time to ensure precision during installation.
Best Practices for Grease Application
Lubrication frequency varies based on usage intensity. For example, construction equipment may need greasing daily, while low-use components can be maintained weekly. Use a grease gun to apply lubricant until fresh grease appears at the joint, avoiding over-lubrication that can attract contaminants.
Signs of improper use include dry, noisy joints, visible leaks, or difficulty in pumping grease. Regular inspection and adherence to manufacturer guidelines help prevent these issues and maintain system efficiency.
Troubleshooting Common Issues
Leaking grease fittings often result from over-tightening, damaged seals, or using incorrect grease. To fix, remove the fitting, inspect it for wear, and replace if necessary. Clogged fittings can be cleared with a wire or compressed air, but severe blockages require replacement.
Worn-out fittings should be replaced when threads are damaged, corrosion occurs, or leakage persists despite cleaning. Proactive replacement prevents larger mechanical issues and ensures consistent lubrication.
FAQ: Frequently Asked Questions About Grease Fittings
What is the difference between a grease fitting and a grease nipple? The terms are interchangeable; both refer to the small valve used to inject grease. However, “zerk” is a brand name that has become generic for standard grease fittings.
How often should grease fittings be lubricated? Follow manufacturer recommendations, but general guidelines suggest weekly maintenance for light use and daily for heavy-duty equipment. High-vibration environments may require more frequent attention.
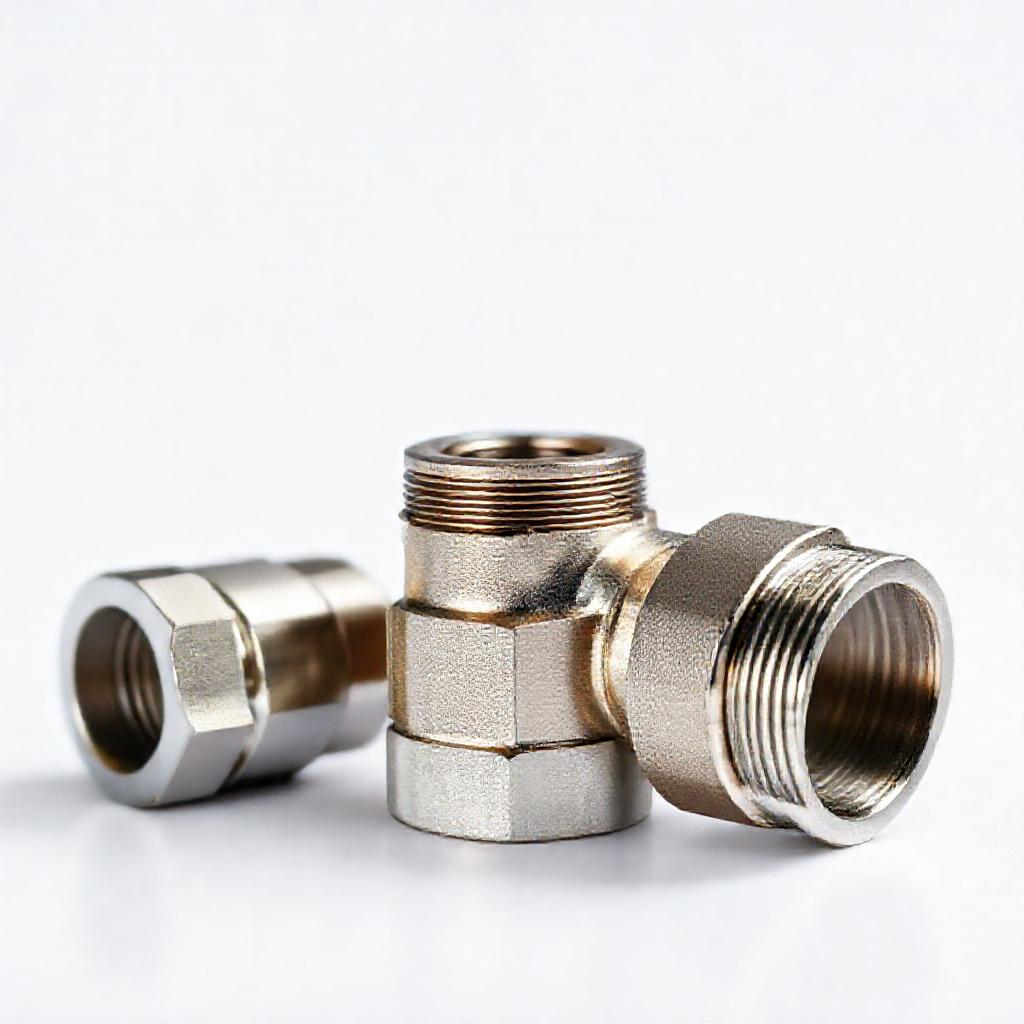
Can I use any type of grease with a standard grease fitting? While standard fittings work with most greases, always confirm compatibility. High-temperature or specialized greases may require specific fitting materials to avoid leaks or degradation.
Why is my grease fitting leaking, and how can I fix it? Leaks often stem from loose or damaged fittings. Tighten the fitting using a wrench, and replace it if the threads are stripped or the seal is compromised. Avoid over-greasing, which can force grease past seals.
Are stainless steel grease fittings better than brass ones? Stainless steel fittings are more resistant to corrosion and suited for harsh environments. Brass is cost-effective but less durable in wet or chemical-heavy settings. Choose based on the operating conditions.
Conclusion
Grease fittings are essential for maintaining the health of machinery and vehicles, acting as the first line of defense against wear and failure. Understanding their types, proper installation, and maintenance ensures optimal performance across industries. Whether in a car, factory, or construction site, these small components play a big role in equipment longevity.
Choose the right fitting material and size for your application, follow lubrication best practices, and address issues promptly to avoid breakdowns. By prioritizing proper grease fitting care, you safeguard your machinery’s efficiency and reliability. Embrace these practices to maximize your equipment’s lifespan and minimize downtime.