Can I Use Regular Sockets on Impact Wrench
Impact wrenches have become indispensable tools in garages, construction sites, and industrial settings, thanks to their ability to deliver high torque with minimal effort. However, one common question that arises is whether regular sockets can be used with these powerful tools. While it might seem convenient to use the sockets you already own, doing so can lead to serious consequences, including tool damage, fastener stripping, or even personal injury. To ensure safety and efficiency, it’s crucial to understand the key differences between regular and impact sockets, including torque strength, material composition, and design features. This guide will explore these factors in detail, helping you make informed decisions about your tool setup.
Step-by-Step Process
Check Socket Type
Verify if sockets are impact-rated for high torque.
Match Drive Size
Ensure socket drive size matches wrench (1/4", 3/8", 1/2").
Assess Torque Rating
Compare socket's torque limit to wrench's output.
Inspect for Damage
Look for cracks or wear in regular sockets before use.
Use Socket Holder
Secure regular sockets with a holder if necessary.
Process infographic for Can I Use Regular Sockets on Impact Wrench
Understanding Impact Wrench Mechanics
What is an Impact Wrench and How Does It Work?
An impact wrench is a power tool designed to deliver high rotational force, or torque, through a combination of rotational motion and hammering action. This mechanism allows it to loosen or tighten bolts and nuts quickly, making it ideal for automotive repairs, construction projects, and heavy machinery maintenance. Unlike regular drills or ratchets, impact wrenches generate a sudden, intense force that can handle stubborn fasteners with ease.
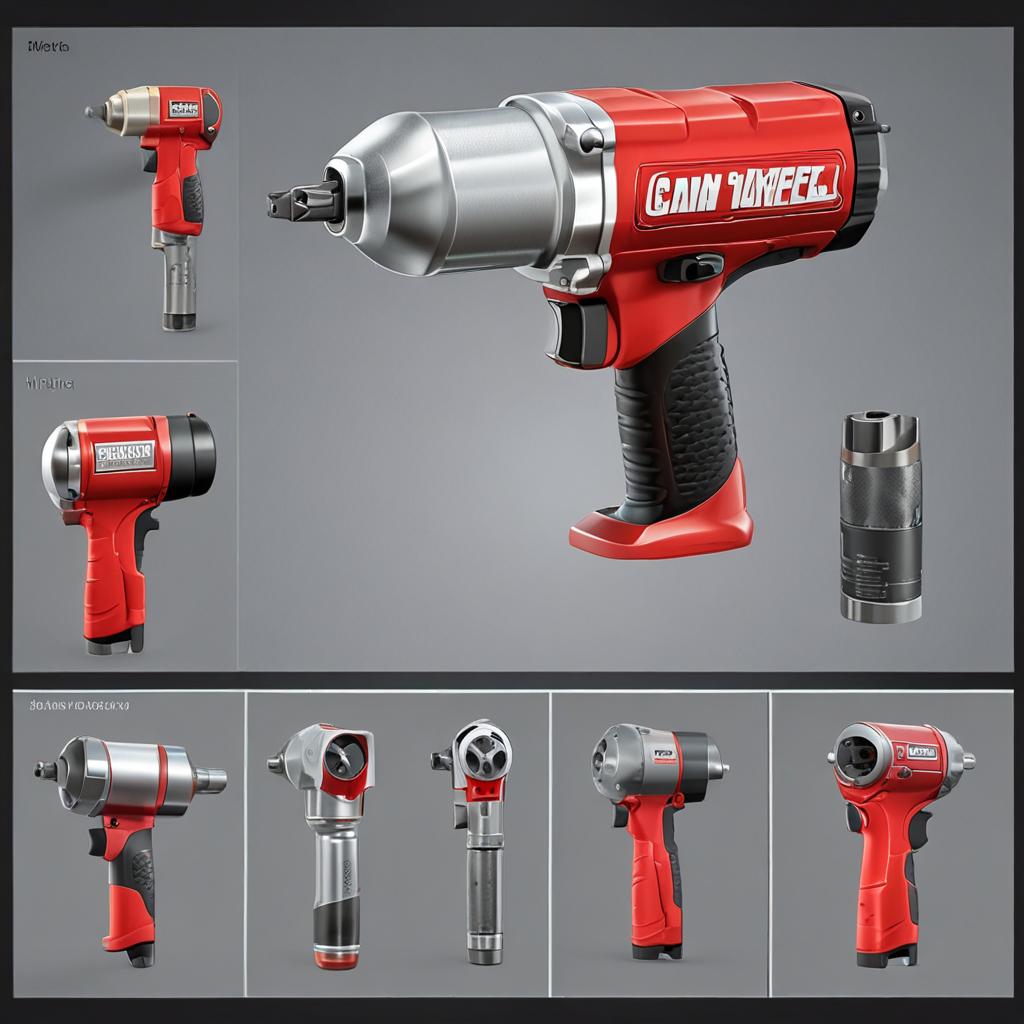
The Torque and Force Generated by Impact Wrenches
Impact wrenches can produce torque ranging from 500 to 1,500 foot-pounds, far exceeding the capabilities of hand tools or standard power tools. While this makes them highly effective, it also increases the risk of over-tightening or damaging fasteners if the wrong sockets are used. The repeated impact forces can cause regular sockets to crack or fail, posing safety hazards and reducing the tool’s efficiency.
Regular Sockets vs. Impact Sockets
What Are Regular Sockets Made Of?
Regular sockets are typically made from chrome vanadium steel, a durable material suitable for hand tools and low-torque applications. However, this material is not designed to withstand the shock and vibration generated by impact wrenches. Over time, the constant stress can cause the socket to deform, crack, or shatter.
What Makes Impact Sockets Different?
Impact sockets are crafted from chrome molybdenum steel, a tougher and more resilient material that can absorb the high forces produced by impact wrenches. They also feature thicker walls, a square drive design, and undergo heat treatment to enhance their durability. These characteristics make them better suited for heavy-duty applications and reduce the risk of failure.
Key Differences to Watch For
- Material toughness: Impact sockets are made to handle shock and vibration, while regular sockets are not.
- Socket dimensions: Impact sockets have thicker walls to prevent cracking.
- Safety certifications: Look for ISO or ASME markings to ensure compliance with industry standards.
Risks of Using Regular Sockets on an Impact Wrench
Socket Cracking or Breaking
Regular sockets are not built to withstand the repeated high-impact forces of an impact wrench. This can lead to cracking or breaking, which not only damages the socket but also poses a safety risk from flying debris.
Stripped Fasteners and Tool Damage
Using regular sockets can result in stripped bolts or nuts due to improper force distribution. Additionally, the impact wrench’s drive mechanism may suffer damage from the increased stress, leading to costly repairs or replacements.
Reduced Efficiency and Performance
Incompatible sockets may slip or wear out faster, making tasks more time-consuming and less effective. This can be particularly frustrating in professional settings where efficiency is key.
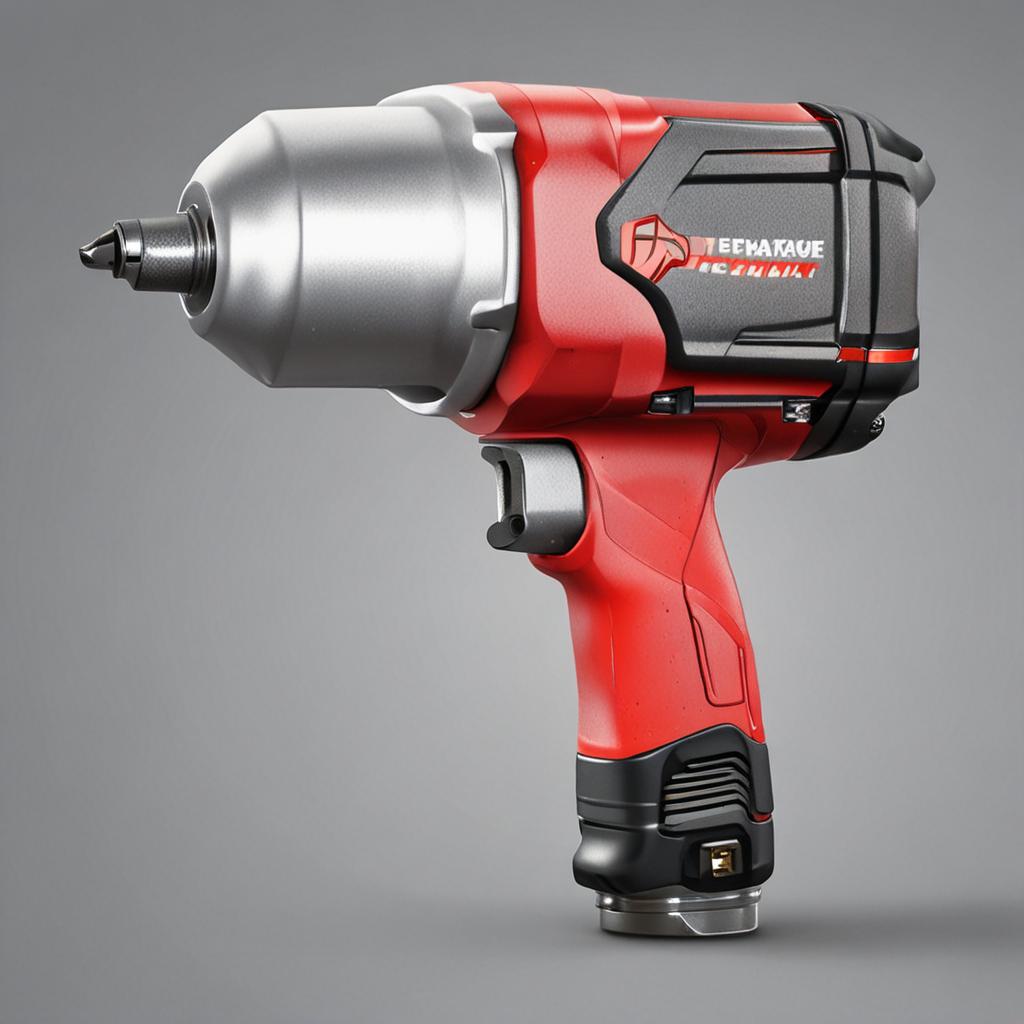
When It’s Technically Acceptable to Use Regular Sockets
Low-Torque Applications
For low-torque tasks, such as removing lug nuts on older vehicles or working with small hardware, regular sockets may suffice. However, this is only a temporary solution and not recommended for heavy-duty use.
Short-Term or Emergency Use Only
In emergencies, regular sockets can be used briefly, but they should not be relied upon for prolonged or high-torque applications. Always prioritize safety and replace them with impact-rated sockets as soon as possible.
Limitations and Cautions
Avoid using regular sockets for high-torque tasks, such as torque-to-yield bolts or heavy machinery, as the risk of failure is significantly higher in these scenarios.
Best Practices for Socket Use with Impact Wrenches
Always Use Impact-Grade Sockets
Invest in sockets labeled “impact-rated” or made from chrome molybdenum steel to ensure compatibility and durability.
How to Identify Impact Sockets
Look for markings like “I” or “Impact,” a matte finish, or specifications such as “1000 Ft-Lbs” to confirm the socket’s suitability for impact wrenches.
Socket Maintenance and Inspection
Regularly inspect your sockets for cracks, warping, or wear to maintain safety and extend their lifespan. Replace any damaged sockets immediately.
Matching Socket Sizes to the Wrench
Ensure the socket’s drive size (1/4”, 3/8”, 1/2”) matches your impact wrench to prevent slippage and ensure optimal performance.
Alternatives to Impact Sockets
Socket Material Upgrades
Consider titanium or alloy sockets for a lighter yet durable alternative to traditional impact sockets.
Adaptors and Extensions
Use a socket adapter to reduce stress on non-impact sockets if absolutely necessary, but exercise caution and limit use to low-torque tasks.
Hand Tools for Precision Work
For tasks requiring accuracy, switch to a torque wrench or ratchet to avoid over-tightening and ensure proper fastener tension.
Conclusion
Using regular sockets on an impact wrench may seem like a quick fix, but it comes with significant risks, including tool damage, fastener stripping, and safety hazards. Impact sockets, designed specifically for high-torque applications, offer the durability and reliability needed to handle the intense forces generated by these tools. By investing in impact-grade sockets and following best practices, you can ensure safer, more efficient, and longer-lasting performance. Always consult manufacturer guidelines and prioritize safety when selecting tools and accessories for your projects.
FAQ Section
Can I use regular SAE sockets on an air-powered impact wrench?
No, they may crack or round edges due to high torque and vibration.
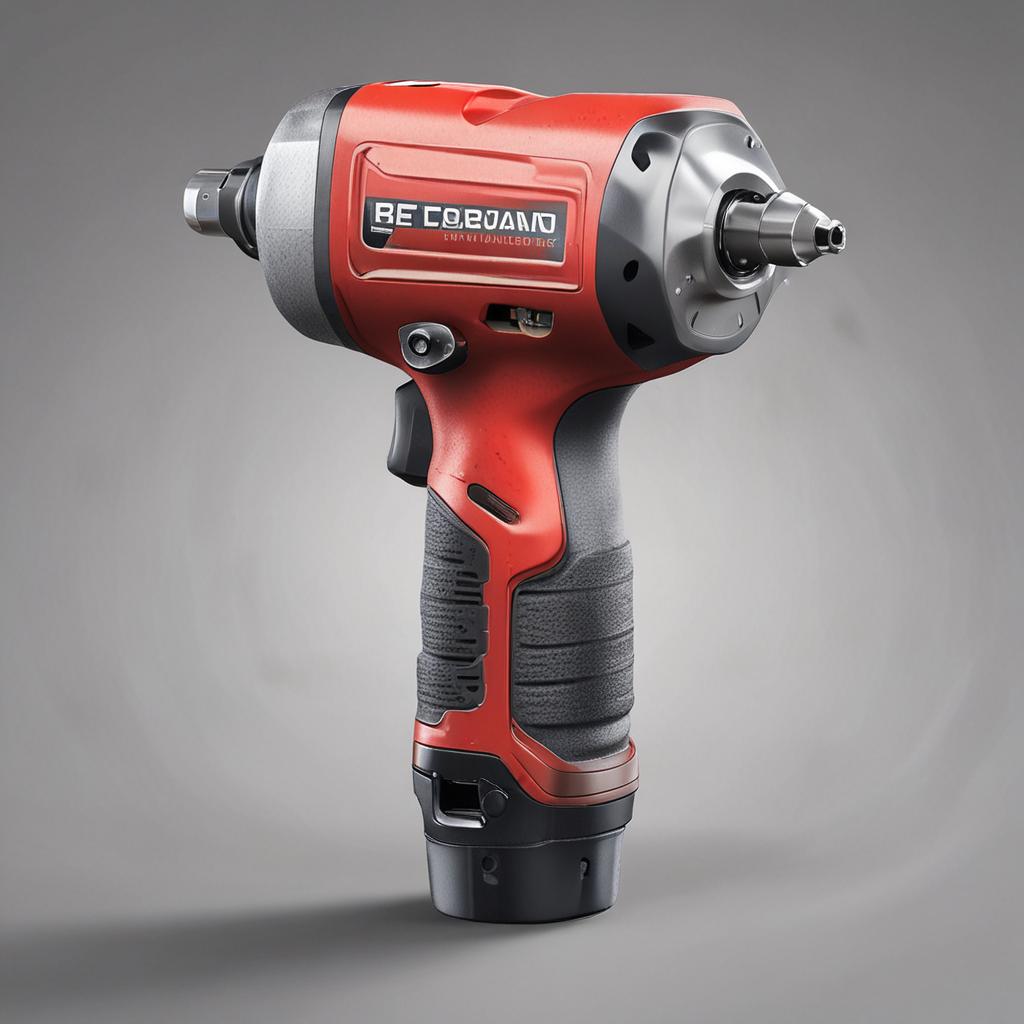
How can I tell if my socket is impact-rated?
Look for clear markings like “Impact,” “I,” or “1000 Ft-Lbs” and a matte finish.
Will using regular sockets void my impact wrench warranty?
Possibly, as tool damage from incompatible sockets may not be covered.
What are the safest materials for impact sockets?
Chrome molybdenum steel or hardened alloys designed to absorb shock.
Are there any tasks where regular sockets work just fine with an impact wrench?
Only for low-torque jobs, like small hardware, but not for automotive or heavy-duty use.