In the world of precision engineering and compact machinery, miniature universal joints play a crucial role in enabling smooth torque transmission in tight spaces. These small yet powerful components are essential in industries where space constraints and high performance are critical. Whether in robotics, medical devices, or advanced consumer electronics, miniature universal joints ensure efficient power transfer while maintaining flexibility and reliability. As technology evolves, the demand for these precision components continues to grow, making them indispensable in modern engineering.
What Are Miniature Universal Joints?
Universal joints, also known as U-joints, are mechanical couplings that allow rotational motion to be transmitted between two shafts that are not aligned. Miniature universal joints are compact versions of these couplings, designed for applications where space is limited but precision and efficiency remain paramount. Their small size makes them ideal for use in intricate machinery and small-scale devices, where traditional universal joints would be impractical.
These joints are particularly important in fields like robotics, medical technology, and automation, where accuracy and reliability are non-negotiable. By enabling flexible power transmission in confined spaces, miniature universal joints help engineers overcome design challenges and enhance the performance of advanced systems.
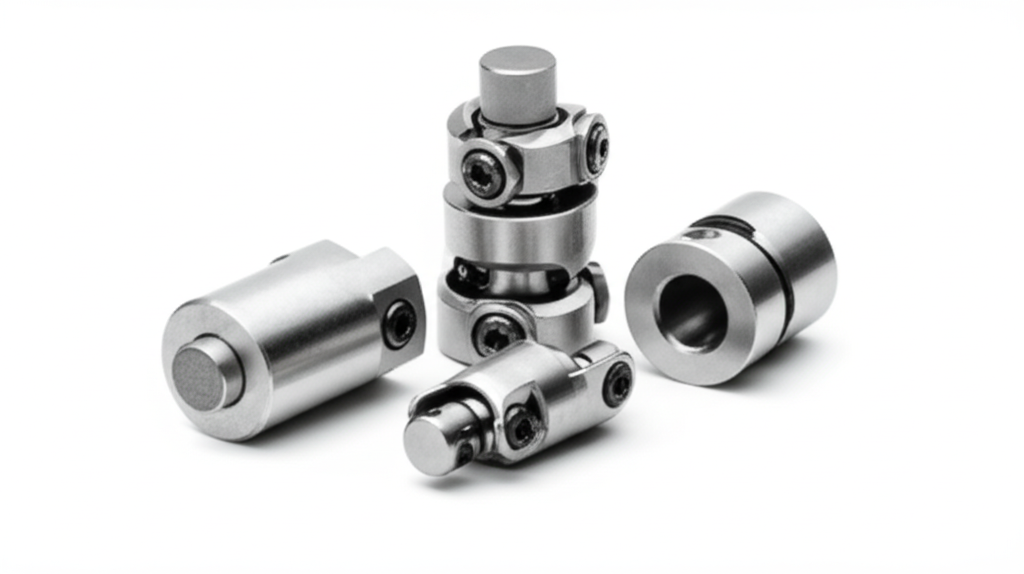
How Miniature Universal Joints Work
Basic Design and Components
Miniature universal joints consist of several key components: yokes, a cross (or spider), and bearings. The yokes attach to the input and output shafts, while the cross connects the two yokes, allowing them to rotate independently. Bearings within the cross ensure smooth movement and reduce friction. Together, these components enable torque transmission even when the shafts are misaligned, making the joint highly versatile.
The design allows for angular misalignment between the shafts, which is essential in applications where flexibility is required. The precise engineering of these components ensures minimal energy loss and maximum efficiency, even at high speeds.
Types of Miniature Universal Joints
Miniature universal joints come in various types, each suited to different applications. Single joints are the most common and consist of one cross and two yokes. Double joints, also known as Cardan joints, feature two crosses and four yokes, providing greater flexibility for complex misalignments. Additionally, these joints can be made from different materials, including steel for high-strength applications, aluminum for lightweight needs, and plastic for cost-effective solutions.
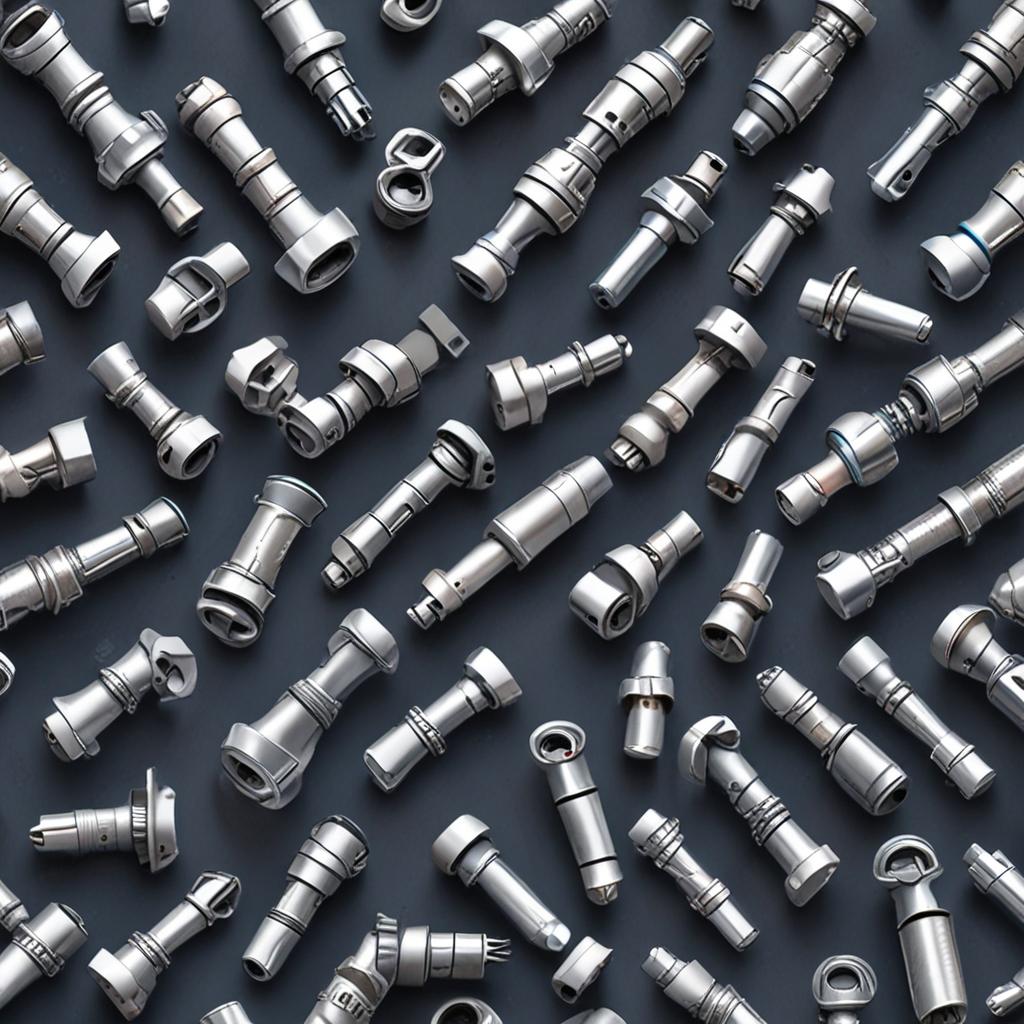
Custom designs are also available, allowing engineers to tailor the joint to specific requirements, such as extreme temperatures, corrosive environments, or unusual load conditions.
Applications of Miniature Universal Joints
Industrial Machinery
In industrial settings, miniature universal joints are used in robotics, CNC machines, and automation systems. Their compact size allows them to fit into tight spaces while maintaining high precision, making them ideal for complex assembly lines and precision manufacturing processes. Their ability to transmit torque efficiently also reduces wear and tear on other components, improving overall system reliability.
Automotive and Aerospace
The automotive and aerospace industries rely on miniature universal joints for steering systems, control mechanisms, and small actuators. In vehicles, these joints help transmit power from the transmission to the wheels, even when the drivetrain is misaligned. In aerospace, they are used in control surfaces and landing gear systems, where space and weight are critical factors.
Medical Devices
Medical applications include surgical tools and diagnostic equipment, where precision and reliability are paramount. Miniature universal joints enable flexible movement in endoscopes, robotic surgical arms, and imaging devices, allowing for precise control in confined spaces. Their compact design and high durability make them essential in life-saving medical technologies.
Consumer Electronics
From cameras to drones, miniature universal joints enhance the functionality of consumer electronics. They allow for smooth and precise movements in camera gimbal systems, ensuring stable footage even in challenging conditions. In drones, these joints help adjust the pitch and yaw of the rotors, improving flight stability and control.
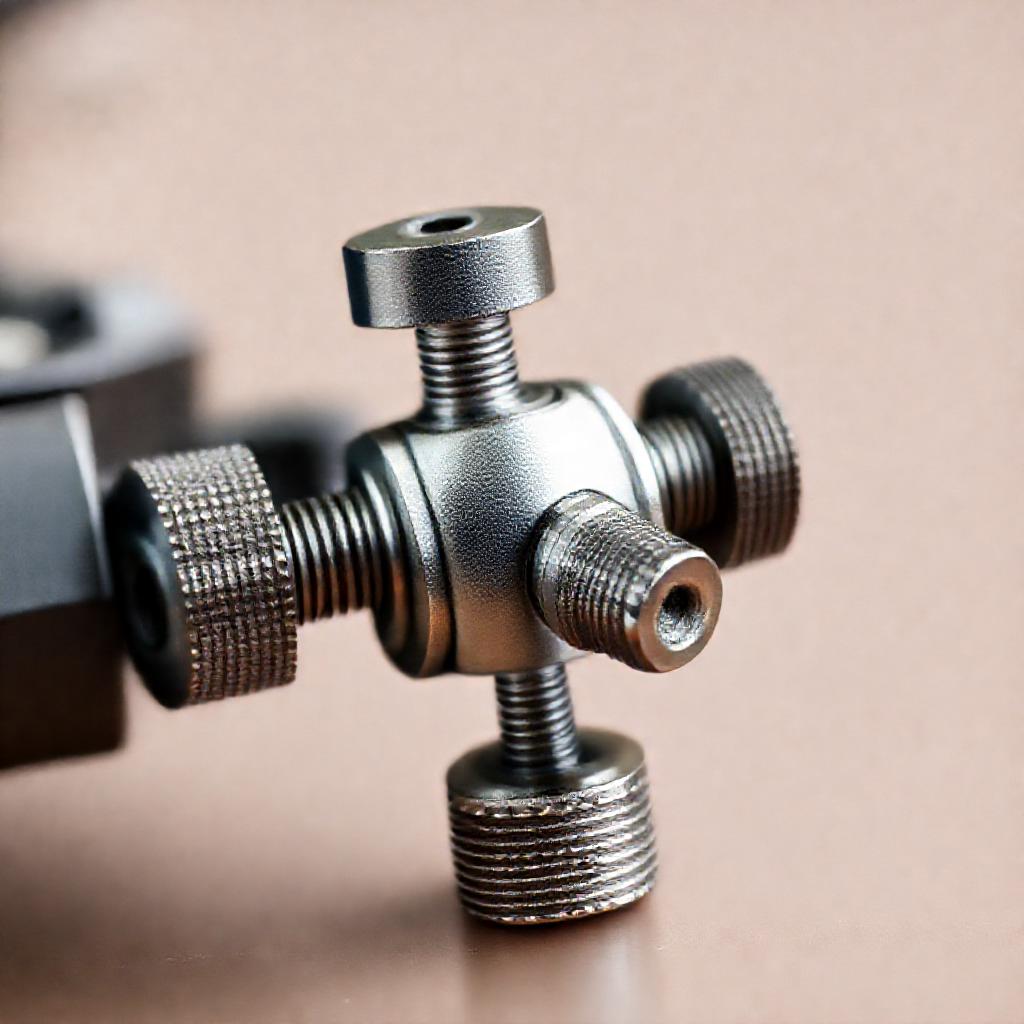
Advantages of Miniature Universal Joints
Compact Size and Flexibility
One of the biggest advantages of miniature universal joints is their small size, which allows them to be used in applications with limited space. Their flexibility in accommodating angular misalignment makes them ideal for complex mechanical systems where traditional joints would not fit. This compactness also reduces the overall weight of the system, which is crucial in applications like drones and medical devices.
High Precision and Efficiency
Miniature universal joints are designed to transmit torque with minimal energy loss, ensuring high efficiency. Their precision engineering allows for accurate motion control, which is essential in applications requiring fine adjustments, such as robotics and medical devices. The smooth operation of these joints also reduces vibrations and noise, enhancing the performance of sensitive equipment.
Durability and Reliability
Built to withstand demanding conditions, miniature universal joints are highly durable and reliable. Their robust construction and high-quality materials ensure a long lifespan, even in harsh environments. Regular maintenance and proper lubrication further extend their operational life, making them a cost-effective solution for long-term use.
Choosing the Right Miniature Universal Joint
Factors to Consider
When selecting a miniature universal joint, several factors must be considered. Torque requirements, speed, and angular misalignment are critical factors that determine the joint’s suitability for a given application. Additionally, material compatibility with the operating environment—such as temperature, humidity, and exposure to chemicals—plays a significant role in ensuring optimal performance. Finally, size and weight constraints must be carefully evaluated to ensure the joint fits within the system’s design specifications.
Customization Options
For applications with unique requirements, customization options are available. Manufacturers can tailor the design of miniature universal joints to meet specific torque, speed, and environmental needs. Custom materials, coatings, and lubrication solutions can also be applied to enhance performance in specialized environments. Working with a reputable supplier ensures that the joint is optimized for the intended application.
Maintenance and Care for Miniature Universal Joints
Regular Inspection and Lubrication
Proper maintenance is essential for ensuring the longevity and performance of miniature universal joints. Regular inspections help identify early signs of wear, such as excessive vibration or unusual noise. Lubrication is also critical, as it reduces friction and prevents premature failure. Using the manufacturer-recommended lubricant and following a scheduled maintenance plan can significantly extend the joint’s lifespan.
Signs of Wear and When to Replace
Common signs of wear in miniature universal joints include increased vibration, grinding noises, and reduced efficiency in torque transmission. If these symptoms are observed, the joint should be inspected and replaced if necessary. Ignoring these signs can lead to further damage to the system and potential failure. Replacing worn joints promptly ensures continued reliability and performance.
The Future of Miniature Universal Joints
The future of miniature universal joints is bright, with ongoing advancements in materials, design, and manufacturing techniques. Innovations in lightweight materials and advanced coatings are enhancing their performance in extreme environments. Additionally, the growing demand for automation, robotics, and miniaturized electronics is driving the development of even more compact and efficient joints. As technology continues to evolve, miniature universal joints will remain a critical component in modern engineering.
FAQ Section
What is the difference between a universal joint and a miniature universal joint?
Comparison table for What is the difference between a universal joint and a miniature universal joint?
The primary difference lies in size and application. Traditional universal joints are larger and designed for heavy-duty applications, such as automotive drivetrains. Miniature universal joints are smaller, allowing them to fit into compact devices like robotics, medical tools, and consumer electronics.
Can miniature universal joints handle high torque?
Yes, miniature universal joints can handle high torque, but their capacity depends on the design and materials used. High-strength steel joints are ideal for heavy-duty applications, while lighter materials like aluminum are suited for lower torque requirements.
Are miniature universal joints suitable for high-speed applications?
Miniature universal joints can be used in high-speed applications, but their performance depends on factors like lubrication, bearing quality, and material strength. Properly designed joints with high-quality bearings can handle high speeds efficiently.
How do I know which material to choose for my application?
The choice of material depends on the operating environment and load requirements. Steel is ideal for high-strength applications, while aluminum is preferred for lightweight needs. Plastic joints are suited for cost-effective, low-torque applications.
Can miniature universal joints be customized for specific needs?
Yes, manufacturers offer customization options to tailor miniature universal joints to specific applications. Custom designs can include specialized materials, coatings, and lubrication solutions to meet unique performance requirements.