Socket head cap screws are essential fasteners in countless mechanical and structural applications, prized for their compact design and high tensile strength. From automotive engines to aerospace components, these screws provide reliable performance in tight spaces where precision is critical. However, their effectiveness hinges on proper tightening, which is where torque charts become invaluable. Understanding and applying the correct torque ensures safety, prevents component failure, and extends the lifespan of your assembly. This guide demystifies torque charts for socket head cap screws, offering practical insights to help you optimize your fastening processes.
Step-by-Step Process
Identify Screw Specs
Determine material, size, and thread type of the socket head cap screw.
Select Torque Chart
Choose the appropriate torque chart based on screw material and coating.
Apply Correct Torque
Use a calibrated torque wrench to tighten the screw to the specified value.
Verify Tightness
Check for proper seating and re-torque if necessary to prevent loosening.
Document Results
Record torque values and any adjustments made for future reference.
Process infographic for Socket Head Cap Screw Torque Chart
What is a Socket Head Cap Screw?
A socket head cap screw is a type of fastener with a cylindrical head and an internal hexagonal socket for driving. Its design allows for high-strength applications while maintaining a low profile, making it ideal for use in machinery, vehicles, and equipment where space is limited. The internal hex drive offers a secure grip, reducing the risk of stripping compared to other head types.
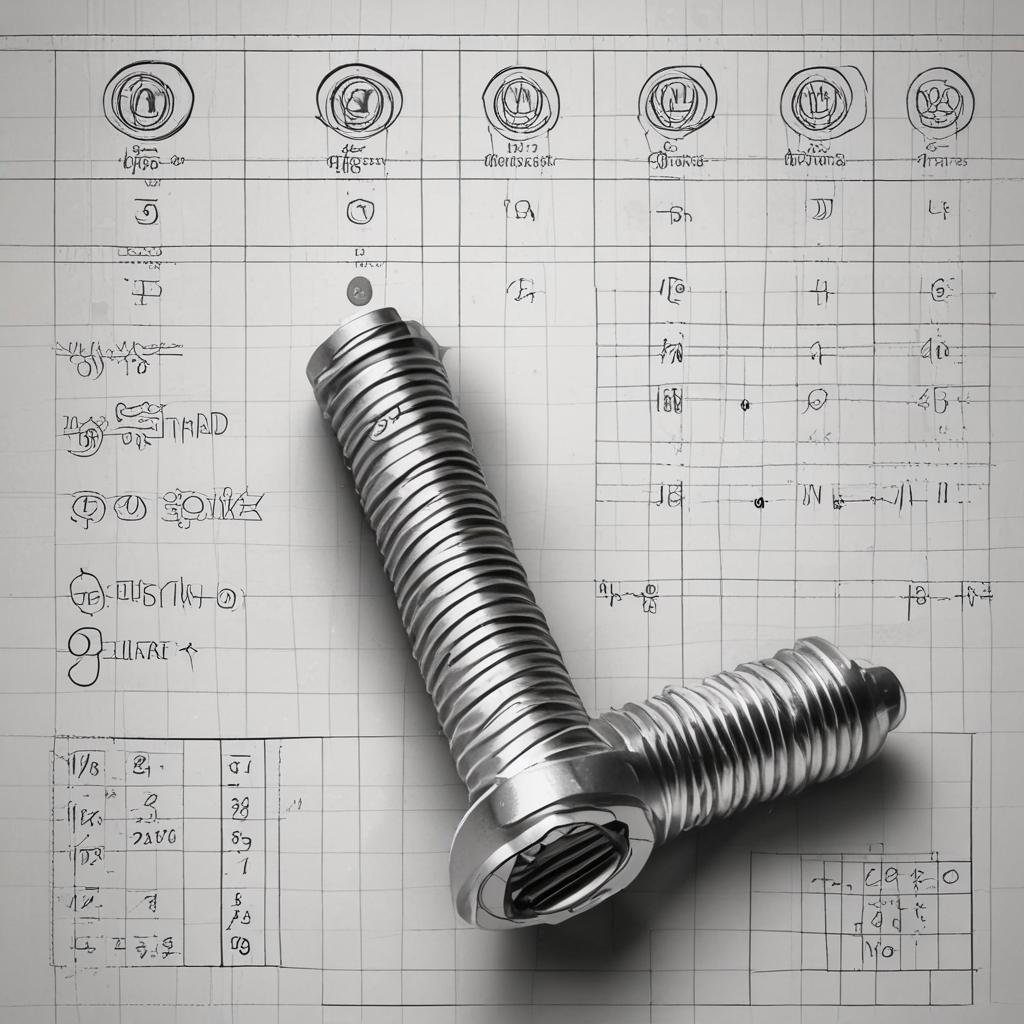
These screws are commonly used in automotive suspension systems, aerospace structures, robotics, and construction hardware. Their ability to withstand significant shear and tensile forces makes them a preferred choice for high-vibration environments. Additionally, socket head cap screws are available in various grades and materials to suit specific load requirements and corrosion resistance needs.
Understanding Torque and Its Importance
Torque refers to the rotational force applied to fasten a screw, measured in units like Newton-meters (Nm) or pound-feet (lb-ft). It plays a crucial role in achieving the correct clamping force to hold components together without causing damage. Proper torque ensures the joint remains intact under stress, preventing loosening or overloading.
Under-tightening leaves the joint vulnerable to vibration, thermal expansion, or external forces, which can lead to slippage or failure. Over-tightening, conversely, risks deforming the screw or stripping threads, potentially causing catastrophic breakage. Balancing these extremes is key to maintaining mechanical integrity and operational safety.
Factors Affecting Torque Requirements
Material of the Screw and Joint
The materials involved—such as steel, aluminum, or titanium—directly influence torque values. Steel screws, for instance, have higher tensile strength than aluminum, requiring different torque specifications to avoid deformation. The joint material also affects friction, which can alter the actual clamping force achieved.
Thread Size and Pitch
Larger thread sizes and finer pitches generally require higher torque due to increased surface area and friction. For example, an M10 screw with a 1.5mm pitch will have a different torque rating than an M10 screw with a 1.25mm pitch, as the latter demands more precise control to achieve optimal tension.
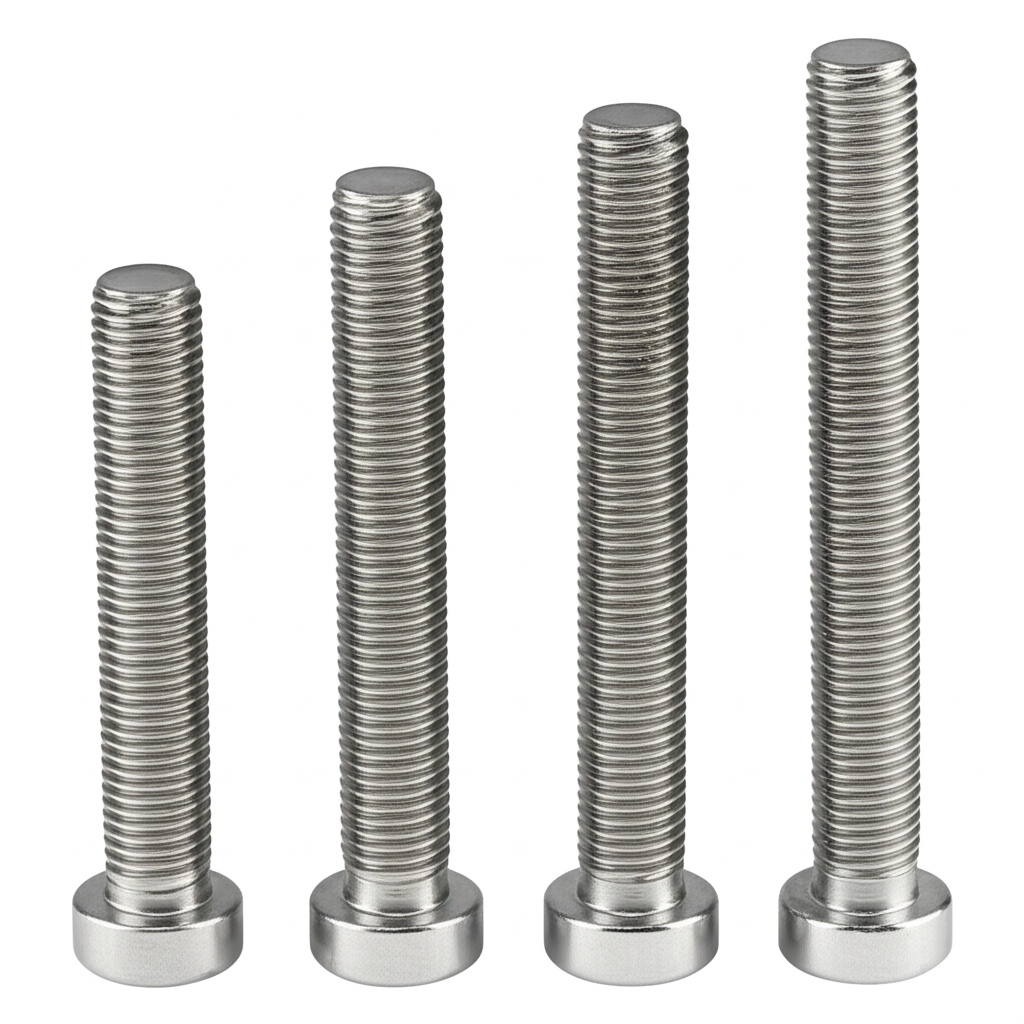
Lubrication
Lubrication reduces friction between the screw threads and the joint, significantly impacting torque. A lubricated screw may need 20–30% less torque than a dry one to achieve the same clamping force. Always check if the torque chart accounts for lubrication and specify the correct type and amount.
Surface Finish
Rough or uneven surfaces increase friction, requiring higher torque values. Conversely, polished or coated finishes reduce friction, altering the necessary force. Adjust your torque application accordingly to compensate for surface variations.
Environmental Conditions
Temperature extremes, humidity, and exposure to corrosive elements can weaken materials or change friction characteristics. For example, high-temperature environments may necessitate using heat-resistant materials and recalibrating torque values to maintain reliability.
How to Use a Socket Head Cap Screw Torque Chart
A torque chart typically lists screw size, thread pitch, material grade, and corresponding torque values. Begin by identifying the screw’s specifications, such as M4 or #8, and its material (e.g., Grade 8 or A2 stainless steel). Cross-reference these details with the chart to find the recommended value.
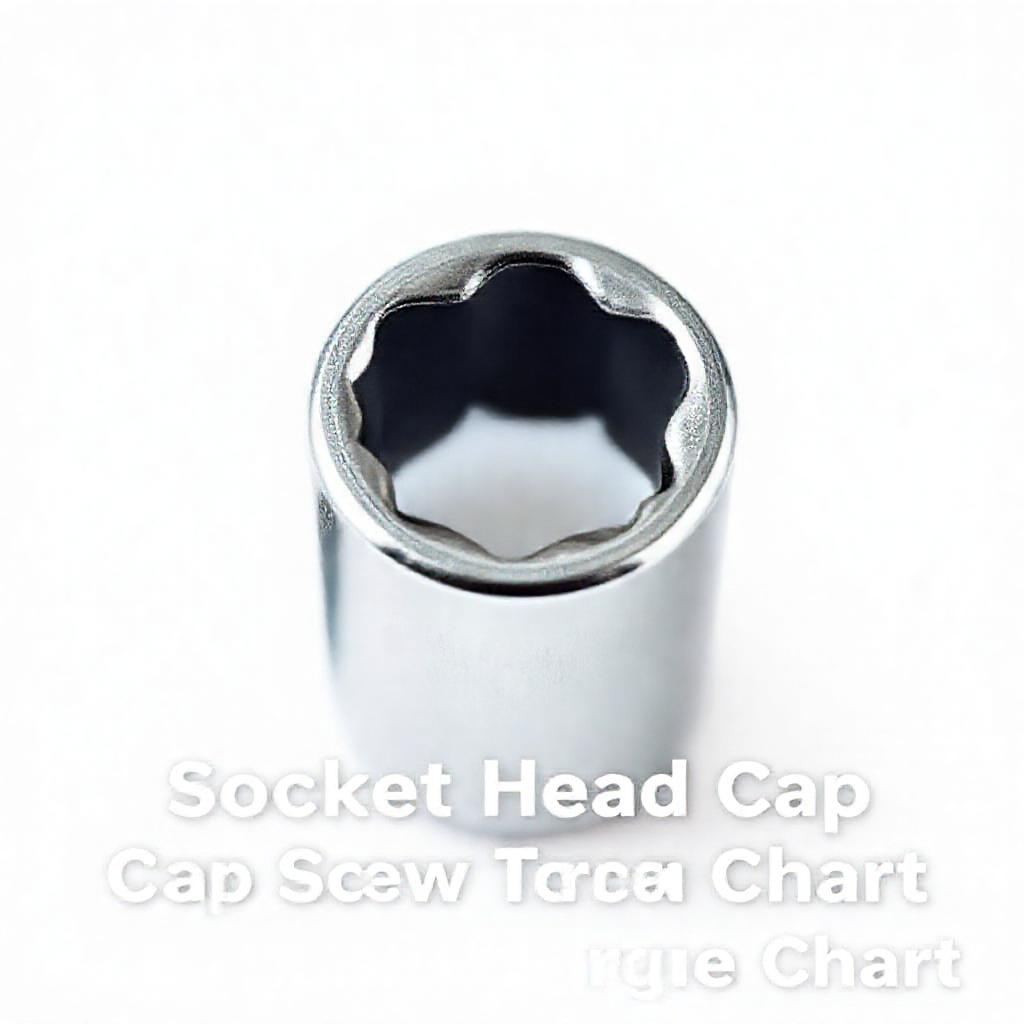
Ensure the chart aligns with the joint material and lubrication conditions. For instance, a chart for steel screws on aluminum threads may include adjusted values to prevent galling. Always verify the units (Nm or lb-ft) and use a calibrated torque wrench for precise application.
Socket Head Cap Screw Torque Chart (Sample)
Here’s a simplified example of torque recommendations for common sizes and materials:
- M3 (0.5mm pitch): Steel – 1.5 Nm (1.1 lb-ft); Aluminum – 0.8 Nm (0.6 lb-ft)
- M5 (0.8mm pitch): Steel – 4.2 Nm (3.1 lb-ft); Stainless Steel – 3.5 Nm (2.6 lb-ft)
- M6 (1.0mm pitch): Steel – 7.0 Nm (5.2 lb-ft); Titanium – 5.5 Nm (4.0 lb-ft)
- M8 (1.25mm pitch): Steel – 18.0 Nm (13.3 lb-ft); Brass – 9.0 Nm (6.6 lb-ft)
These values are approximate and depend on lubrication, surface finish, and application conditions. Always consult manufacturer guidelines for exact specifications.
Tips for Applying the Correct Torque
- Use a calibrated torque wrench to avoid over- or under-tightening.
- Apply recommended lubricants as specified in the torque chart to maintain consistency.
- Replace damaged screws immediately; reusing them can compromise joint integrity.
- Inspect fasteners regularly, especially in high-vibration or high-load scenarios, to ensure torque retention.
Common Mistakes to Avoid
- Guessing torque values instead of referencing a chart can lead to inconsistent results and failures.
- Ignoring environmental factors like temperature or corrosion may cause unexpected loosening or material degradation.
- Using uncalibrated or improper tools, such as regular wrenches instead of torque wrenches, increases the risk of errors.
- Overlooking thread engagement depth can result in insufficient clamping force or stripped threads.
Conclusion
Socket head cap screws demand precise torque application to ensure safety and performance. By understanding the factors that influence torque and using a reliable chart, you can avoid costly mistakes and extend the life of your mechanical assemblies. Always match your screw specifications to the chart data and stay mindful of environmental and installation variables. Prioritizing accuracy in tightening practices will pay dividends in long-term reliability.
FAQ Section
1. What is the purpose of a socket head cap screw torque chart?
A torque chart provides recommended torque values for specific screw sizes and materials, ensuring proper tightening and preventing damage.
2. How do I determine the correct torque value for my screw?
Refer to the torque chart based on the screw’s size, material, and thread pitch. Ensure alignment with the joint material and lubrication conditions.
3. Can I use the same torque for all socket head cap screws?
No, torque values vary depending on screw size, material, and application. Always consult the torque chart for accurate values.
4. What happens if I over-tighten a socket head cap screw?
Over-tightening can strip threads, damage the screw or joint, and lead to mechanical failure.
5. Is lubrication necessary when applying torque?
Yes, lubrication reduces friction and ensures accurate torque application. However, the type and amount of lubricant should align with the torque chart recommendations.